Furthermore, the methodology of the self-adaptation in order to achieve resilience is examined. Consequently, adjusting valves are used in the FDA.
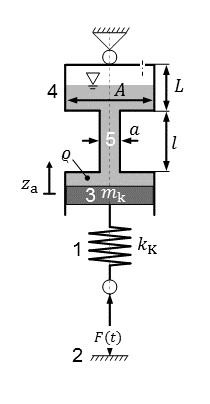
By the use of the FDA, vibrations in a defined frequency band of a basic system can be reduced. Energy is redirected into the structure extension. The FDA (Fig. 1) consists of a spring 1 which connects the structure to be soothed 2 to a piston 3. When the piston is immersed, liquid is displaced into a second cylinder chamber 4 via a channel surface 5. The hydraulic transmission between piston and channel area is α:=A/a>1. The light weight principle of the FDA is illustrated by the ratio of heavy mass to the acting inert mass, which is of the order of magnitude of α^(-2) at a small piston mass m_k.
Simulation results from a quarter-vehicle model show that the driving safety of a suspension as a measure of the wheel load fluctuation can be increased by 11 % by integration of the FDA. To confirm this result, the axiomatic model is validated with the functional prototype (Fig. 2) on the servo-hydraulic testing machine.
Subproject Managers
Photo | Name |
---|---|
![]() | Prof. Dr.-Ing. Peter Pelz |